A single inch of measurement error can ruin your product’s packaging fit and appearance completely.
Accurate measurement of custom packaging box dimensions plays a significant role in your business success. Proper box measurements don’t just affect how your product fits – they substantially affect your material costs, shipping expenses, and warehouse storage efficiency.
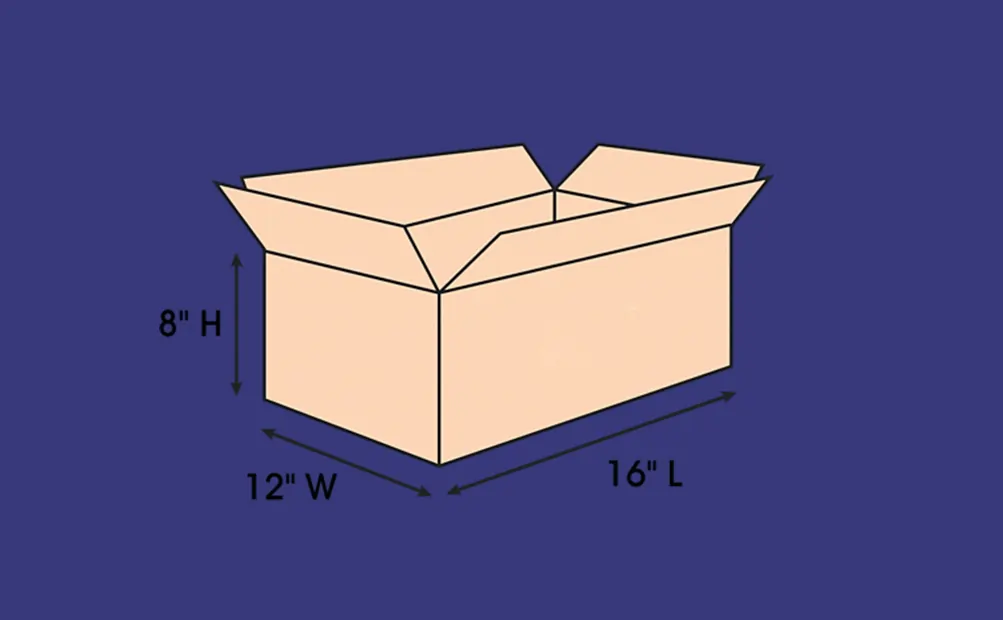
Interior dimensions serve as the industry standard to ensure products fit securely in their packaging. Many businesses make mistakes that get pricey when they overlook this significant detail. This piece will help you measure your custom packaging boxes correctly, every time.
Want to become skilled at precise box measurements and protect your business from expensive packaging mistakes? Let’s tuck into everything you need to know about measuring custom packaging boxes properly.
Essential Tools and Preparation for Box Dimensions
The right tools make box measurements accurate and easy. You’ll need one of these measuring instruments:
- A ruler for small boxes (up to 18 inches)
- A tape measure for medium to large boxes
- A yardstick for larger boxes
- Calipers for precise measurements of small boxes
Your specific needs determine the best measuring tool choice. To cite an instance, tape measures give you flexibility with boxes of all sizes. While digital calipers display clear readouts for detailed measurements.
Accurate measurements start with good preparation. Place your box on a clean, level surface before you measure. This simple step helps you avoid tilted or uneven measurements that could affect your final dimensions.
Custom packaging projects need internal measurements instead of external ones. This method will give a perfect fit for your products inside the box, whatever the material’s thickness. Add a quarter-inch allowance to make items easy to place and remove, and leave room for packaging supplies.
Note that your measuring units should stay consistent. Pick either inches or centimeters and stick with that choice throughout your measurements. This becomes especially important when you have shipping or fitting specifications to meet.
Step-by-Step Guide to Measure Box Dimensions
You need precise measurements to get your custom packaging box dimensions right. This guide will help you measure accurately every time.
Box dimensions follow a standard recording order: length x width x height. Manufacturing and shipping teams use this sequence worldwide to avoid confusion.
The measurement process works like this:
- Measure the Length
- Find the longest side of the box with a flap
- Place your measuring tool from edge to edge
- Record this measurement first
- Measure the Width
- Turn the box 90 degrees
- Measure the shorter side with a flap
- Write down your second measurement
- Measure the Height
- Close all box flaps
- Measure from top to bottom
- Note this final measurement
The box volume calculation comes from multiplying these three measurements (Length x Width x Height). Shipping costs and storage needs depend on this calculation.
Custom packaging projects need internal dimension measurements. Your products will fit perfectly with this method since corrugated boxes add several millimeters to external measurements due to their fluted construction.
A space buffer of 1/8th inch (0.125 in.) should be added to each product dimension. Products stay secure during shipping without getting stuck in tight spaces.
Common Box Measurement Mistakes and Solutions
Our team has seen many mistakes that can hurt your packaging success. Let’s look at these common problems and how to fix them.
The biggest problem we see is mislabeling dimensions. Length × Width × Height is the industry standard notation. Any mix-up in this sequence can get pricey with manufacturing delays and shipping problems.
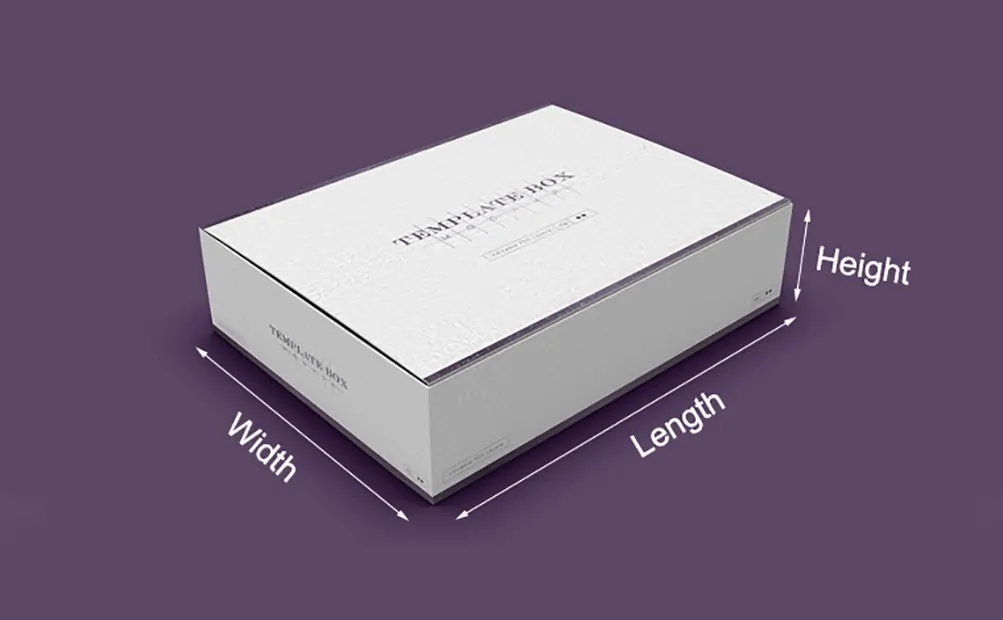
These mistakes come up often:
- Using external measurements instead of internal ones
- Overlooking material thickness, especially in corrugated boxes
- Inconsistent measuring units (mixing inches and centimeters)
- Not accounting for padding materials
- Ignoring box material thickness
The thickness of corrugated cardboard can substantially affect your measurements. Double-walled corrugated boxes with 0.25-inch walls will reduce internal dimensions by 0.5 inches on each axis.
Understanding the difference between internal and external measurements is a vital part of packaging. We recommend measuring internal dimensions to ensure your product fits properly. This becomes even more important with corrugated boxes because the fluted texture between paperboards adds several millimeters to external measurements.
We suggest adding a tolerance of about 1/8 to 1/4-inch to protect product safety. This extra space handles minor irregularities in box construction and measuring techniques.
Conclusion
Accurate box measurements create the foundation of successful custom packaging. This piece demonstrates the impact of proper measuring techniques on product protection, shipping costs, and storage efficiency.
The right measuring tools and a step-by-step process will help you avoid common pitfalls. Your focus should stay on internal dimensions with appropriate allowances that match your specific packaging needs. This approach will give a perfect fit for your products and keep them safe during transit.
Custom packaging success depends on detailed attention and consistent measurement practices. The same measurement principles apply to small product boxes and large shipping containers. These techniques will improve your packaging efficiency and product protection consequently.
FAQs
Q1. How do I correctly measure a custom packaging box?
- To measure a custom packaging box, start with the length (longest side with a flap), then width (shorter side with a flap), and finally height (side without flaps). Always measure internal dimensions and use consistent units throughout.
Q2. What does L x W x H mean in box measurements?
- L x W x H stands for Length x Width x Height, which is the standard notation for box dimensions. Length is the longest side with a flap, width is the shorter side with a flap, and height is the side without flaps.
Q3. Why is it important to measure the internal dimensions of a box?
- Measuring internal dimensions is crucial because it determines whether your product will fit properly inside the box. This is especially important for corrugated boxes, where external measurements can be misleading due to material thickness.
Q4. Should I add extra space when determining the box size for my product?
- Yes, it’s recommended to add about 1/8 to 1/4 inch to each product dimension when determining box size. This extra allowance ensures easy placement and removal of items and accommodates any necessary packaging materials.
Q5. What are common mistakes to avoid when measuring packaging boxes?
- Common mistakes include using external instead of internal measurements, overlooking material thickness, mixing measurement units, not accounting for padding materials, and mislabeling dimensions. Always follow the standard L x W x H notation and consider material thickness, especially for corrugated boxes.